Description
This basic system without the TPx option makes chemisorption and physisorption analyses affordable to even the most modestly funded laboratories. The instrument rapidly and accurately performs pulse chemisorption studies and surface area analyses. The ChemiSorb 2720 features one port dedicated to performing the sorption analysis and a second port designed for sample preparation. It also features a built-in cooling fan for the sample port, four carrier gas inlets, one prep gas inlet, and the optional capability to accommodate a mass spectrometer or other external detector attached at the exhaust port.
In addition to chemisorption experiments that include determining the percent metal dispersion, active metal area, crystallite size, and quantifying acid and base sites, a range of physisorption experiments including BET surface area, Langmuir surface area, and total pore volume can also be conducted. Hands-on calibration and dosing procedures make it an excellent teaching tool for gas-solid surface interaction studies.
The basic instrument (without the ChemiSoft TPx option) provides two ways to collect data: 1) via a front panel meter that may be calibrated to display gas volumes adsorbed onto or desorbed from a sample, and 2) by a chart recorder monitoring the analog output from the thermal conductivity detector.
An optional access fitting allows the ChemiSorb to utilize a mass spectrometer or other external detector for identification of desorbed species or reaction products.
The ChemiSorb 2750
Higher Precision and Versatility
The ChemiSorb 2750 (built upon the same design elements as the Chemisorb 2720) has been further enhanced with the addition of an injection loop for pulsing active gases on the catalyst and features an enhanced dual-port design that allows in-situ preparation and analysis of two samples. Its dual-function sample ports have the capability to be used as either an analysis port or a degas port, eliminating the need to move the sample. This requires less effort and reduces the chances of contaminating an activated sample from exposure to stray gases.
Performing different types of analyses is also easier. In addition to the four carrier gas inlets and three preparation gas inlets, a dedicated gas inlet for the pulse chemisorption gas has been added. Thus the increased number of ports provides a rapid method for gas change overs without the need to manually disconnect, reconnect, and purge gas lines; this further minimizes the risk of contamination and improves the ease of operation.
Higher precision, repeatability, and reproducibility are provided by the incorporation of an injector loop valve in addition to the injection septum. The loops are easily exchanged to provide different injection volumes. Electrically activated inlet valves allow the use of gases containing H2, CO,O2, N2O, NH3, liquid vapor sources, or other adsorptives. Three built-in prep gas inlets and four carrier gas inlets allow for a variety of experiments without having to disconnect, reconnect, and purge gas lines.
ChemiSorb Features | 9605 | 9620 |
---|---|---|
Analysis Ports | 1 | 2* |
Preparation Port | 1 | * |
Injection Septum | ✔ | ✔ |
Injection Loop | ✔ | |
Sample Reactor | Quartz | Quartz |
Gas Inlets | ||
Carrier | 4 | 4 |
Preparation | 1 | 3 |
Loop | 1 | |
Temperature Control | ||
Integrated | 2** | 2* |
Max Temperature | 400 °C | 400 °C |
With TPx Option | 1100 °C | 1100 °C |
Fan-assisted Cooling | 1 | 2 |
Standard Analysis | ||
Pulse Chemisorption | ✔ | ✔ |
Physisorption | ✔ | ✔ |
ChemiSoft TPx Analyses | ||
TPR | ✔ | ✔ |
TPD | ✔ | ✔ |
TPO | ✔ | ✔ |
Pulse Chemisorption | ✔ | ✔ |
Physisorption | ✔ | ✔ |
Loop Calibration | ✔ | |
ChemiSoft TPx Reports | ||
% Metal Dispersion | ✔ | ✔ |
Metal Surface Area | ✔ | ✔ |
Average Crystallite Size | ✔ | ✔ |
First Order Kinetics | ✔ | ✔ |
Single-point Surface Area | ✔ | ✔ |
BET Mulitipoint Surface Area | ✔ | ✔ |
Langmuir Surface Area | ✔ | ✔ |
Total Pore Volume | ✔ | ✔ |
Added Capability – Optional ChemiSoft TPx System
Optional ChemiSoft TPx System (temperature-programmed controller and software) expands the capabilities of the ChemiSorb 2720 and 2750 to include temperature-programmed reactions, data archiving, and advanced data reduction and reporting options. Expanded physisorption capability includes multipoint BET surface area.
* Dual Function Analysis/Preparation
** One dedicated controller for preparation port and one dedicated controller for the analysis port
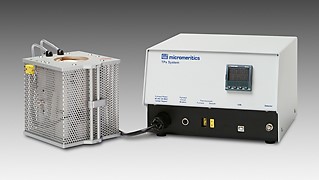
ChemiSorb 2720 / 2750 Applications
Catalysts
The active surface area and porous tructure of catalysts have a great influence on production rates. Limiting the pore size allows only molecules of desired sizes to enter and leave; creating a selective catalyst that will produce primarily the desired product. Chemisorption experiments are valuable for the selection of catalysts for a particular purpose, qualification of catalyst vendors, and the testing of catalyst performance over time to establish when the catalyst should be reactivated or replaced.
Fuel Cells
Platinum-based catalysts including Pt/C, PtRu/C, and PtRuIr/C are often characterized by temperature-programmed reduction to determine the number of oxide phases and pulse chemisorption to calculate:
- Metal surface area
- Metal dispersion
- Average crystallite size
Partial Oxidation
Manganese, cobalt, bismuth, iron, copper, and silver catalysts used for the gas-phase oxidation of ammonia, methane, ethylene, and propylene are characterized using:
- Temperature-programmed oxidation
- Temperature-programmed desorption
- Heat of desorption of oxygen
- Heat of dissociation of oxygen
Catalytic Cracking
Acid catalysts such as zeolites are used to convert large hydrocarbons to gasoline and diesel fuel. The characterization of these materials includes:
- Ammonia chemisorption
- Temperature-programmed desorption of ammonia
- Temperature-programmed decomposition of alkyl amines
- Temperature-programmed desorption of aromatic amines
Catalytic Reforming
Catalysts containing platinum, rhenium, tin, etc. on silica, alumina, or silica-alumina are used for the production of hydrogen, aromatics, and olefins. These catalysts are commonly characterized to determine:
- Metal surface area
- Metal dispersion
- Average crystallite size
Isomerization
Catalysts such as small-pore zeolites (mordenite and ZSM-5) containing noble metals (typically platinum) are used to convert linear paraffins to branched paraffins. This increases the octane number and value for blending gasoline and improves the low temperature flow properties of oil. The characterization of these materials includes:
- Temperature-programmed reduction
- Pulse chemisorption
Hydrocracking, Hydrodesulfurization, and Hydrodenitrogenation
Hydrocracking catalysts typically composed of metal sulfides (nickel, tungsten, cobalt, and molybdenum) are used for processing feeds containing polycyclic aromatics that are not suitable for typical catalytic cracking processes. Hydrodesulphurization and hydrodenitrogenation are used for removing sulfur and nitrogen respectively from petroleum feeds. The characterization of these materials includes:
- Temperature-programmed reduction
- Oxygen pulse chemisorption
Fischer-Tropsch Synthesis
Cobalt, iron, etc. based catalysts are used to convert syngas (carbon monoxide and hydrogen) to hydrocarbons larger than methane. These hydrocarbons are rich in hydrogen and do not contain sulfur or nitrogen. The characterization of these materials includes:
- Temperature-programmed desorption
- Pulse chemisorption
ChemiSorb Theory and Design
The Analytical Technique
The ChemiSorb 2720 and 2750 both utilize the dynamic (flowing gas) technique of analysis. The quantity of gas adsorbed from the gas stream by the sample is monitored by a downstream thermal conductivity detector (TCD). The temperature and pressure at which adsorption/desorption occurs is either known or monitored. The instruments can be used to study physical or chemical adsorption. Preparation usually is accomplished by flowing either an inert or chemically active gas over the sample. After preparation, another gas is selected for analysis. Prep and carrier gases typically used to allow both physical and chemical adsorption experiments are He, Ar, N2, He/N2mixtures, H2, and O2, some serving as both prep and carrier.
Chemical Adsorption
Any of a number of reactive gases such as anhydrous NH3, CO2, CO, H2, N2O, O2, and H2S can be used to react with the active surface. A series of injections of a known quantity of reactive gas is injected into an inert gas stream that passes through the bed of catalysts. Downstream from the reactor is a detector, which determines the quantity of reactive gas that is removed from each injection. Chemisorption tests ideally are made with the sample at a temperature such that only chemisorption occurs. The active surface of the sample is saturated when the detector indicates that the total quantity of subsequent injections passes through the sample bed without any loss. The sum of the injected quantity minus the quantity of gas that passed without adsorption equals the quantity adsorbed.
Unlike physical adsorption, the injected gas chemically adsorbs only on the active surface and not on the support. Thus, the number of gas molecules required to cover the active surface area, once determined, leads directly to the active surface area. Applying the stoichiometry factor for metal reaction yields the number of accessible atoms of active metal. Furthermore, using the total quantity of active metal per gram of catalyst material (determined from the manufacturing formula) leads to the determination of the percent dispersion of active metal. Using the information gathered plus the density of the metal, the size of the metal crystallite can be estimated if it is assumed that these particles have uniform geometry of known volume-to-area ratio.
Physical Adsorption
The surface area of granulated and powdered solids or porous materials is measured by determining the quantity of a gas required to form a monomolecular layer on a sample. Physical adsorption tests typically are performed at or near the boiling point of the adsorbate gas; N2 being most common with a liquid N2 bath being used to maintain the analysis temperature. Under these conditions, a nitrogen and helium mixture of 30 volume percent nitrogen achieves the partial pressure condition most favorable for the formation of a monolayer of adsorbed nitrogen at atmospheric pressure. Under such specific conditions, the area covered by each gas molecule is known within relatively narrow limits. The area of the sample is thus calculable directly from the number of adsorbed molecules, which is derived from the gas quantity at the prescribed conditions, and the area occupied by each. Additionally, atmospheric pressure and ice water temperature may establish appropriate conditions for an n-butane and helium mixture. Other gases at other conditions are also usable.
Chemisorption defined:
Chemical adsorption is an interaction much stronger than physical adsorption. In fact, the interaction is an actual chemical bond where electrons are shared between the gas and the solid surface. While physical adsorption takes place on all surfaces if temperature and pressure conditions are favorable, chemisorption only occurs on certain surfaces and only if these surfaces are clean. Chemisorption, unlike physisorption, ceases when the adsorbate can no longer make direct contact with the surface; it is therefore a single layer process.
ChemiSoft TPx Option
When the optional programmable furnace system and accompanying ChemiSoft TPxsoftware are added to the 2720 or the 2750, another category of chemical adsorption testing can be performed –—Temperature-programmed reactions reduction (TPR),oxidation (TPO), and desorption (TPD).
Temperature control is provided by a furnace that operates from ambient (20 °C) to 1100 °C, and is able to produce temperature ramps of up to 50 °C/min within the 20 to 500 °C range, 30 °C/min within the 500 to 750 °C range, and up to 10 °C/min in the 750 to 1100 °C range. The furnace controller can be programmed to provide multiple ramps and soak times.
Temperature-programmed Chemisorption
Temperature-programmed chemisorption provides information about adsorption strength when a catalyst is at working condition or at an elevated temperature.TPD analyses determine the number, type,and strength of active sites available on the surface of a catalyst from measurement of the amount of gas desorbed at various temperatures. During a TPR analysis, a metaloxide is reacted with hydrogen to form a pure metal. TPR determines the number of reducible species present in the catalyst and reveals the temperature at which reduction occurs. TPO examines the extent to which a catalyst can be reoxidized and measures the degree of reduction of certain oxides.
ChemiSoft TPx Software
Included in the Temperature-Programmed Chemisorption option is Micromeritics’ChemiSoft software that can be used to simplify chemisorption and physisorption aswell as temperature-programmed analyses.The software tracks and records time, monitors and records the analytical temperature and detector output, creates and organizes data files, reduces collected data, and produces a variety of user-defined reports. Advanced peak integration capabilities assure reliable results.
With ChemiSoft, you can create and store standard sets of analysis conditions for guiding frequently performed analyses. Analysis and prep conditions also are reported to provide a record of the environment under which the reported data were collected; this also assures faithful repeating of an experiment if required. Cut-and-paste and data export features simplify moving data to reports or incorporating chemisorption data with data from other analytical techniques.
For the novice operator, the software features prompts for each step in the analysis process, literally talking the user through an analysis sequence. When you are ready to move up to Micromeritics’ more advanced AutoChem 2920 or ASAP 2020 Chemi, or to incorporate other Micromeritics products into your laboratory, your operators will find that the format of the operating software is the same from product to product, thus training time is minimized.
ChemiSoft TPx software can be set up to run independently of the instrument. This means that data files can be reviewed, calculation parameters changed, and reports generated on any computer anywhere, anytime.
Other functions of ChemiSoft
- Allows control of units, axis scales, and reporting range
- Prints report to screen, printer, or file (text only)
- Cut-and-paste capabilities
- Capture displayed plots as a series of x-y coordinates
- Capture tables from screen as ASCII text files
- Integrates detector signals both automati-cally and manually
- Displays and prints peak graphs andreports
- Establishes calibration curves for calculation of unknown sample concentrations
- Reprocess stored analysis data using different parameters
- Exports data in ASCII text format for use in other applications
- Allows for off-line data manipulation
- Provides the ability to monitor two instruments from one computer
- Monitors and records furnace temperature