Description
With this single instrument, you can acquire valuable information about the physical properties of your catalyst, catalyst support, or other materials. It can determine catalytic properties such as percent of metal dispersion, active metal surface area, acid strength, surface acidity, distribution of strength of active sites, BET surface area, and more.
The AutoChem II 2920 performs pulse chemisorption, temperature-programmed reduction (TPR), desorption (TPD), oxidation (TPO), and reaction analyses and does it automatically.
Wide Variety of Features and Benefits:
Chemical adsorption (chemisorption) analyses can provide much of the information needed to evaluate catalyst materials in the design and production phases, as well as after a period of use. The chemical adsorption isotherm reveals information about the active surface of a material have emerged as an indispensable companion to chemisorption isotherm analyses in many areas of industry.
Four internal temperature-controlled zones can be heated independently up to 150 °C. This prevents condensation in the flow path and allows studies to be performed with vapors.
Low internal plumbing volume assures high resolution, fast detector response, and reduces error.
Highly sensitive linear thermal conductivity detector (TCD) assures the calibration volume remains constant over the full range of peak amplitudes so the area under the peak is directly proportional to the volume of gas reacted.
Four high-precision mass flow controllers provide extremely accurate, programmable gas control.
Corrosion-resistant detector filaments are compatible with most destructive gases and reduce the likelihood of filament oxidation.
Clamshell furnace can heat the quartz sample reactor to 1100 °C. Any number of ramp rates and sequences facilitate customized experiments.
Four gas inlets each for the preparation, carrier, and loop gases permit four-gas sequential experiments, such as TPR/TPO cycles.
Mass spectrometer port and software integration allows virtually simultaneous detection on both the thermal conductivity detector and mass spectrometer.
Optional Vapor Generator permits analysis using vaporized liquids in an inert carrier stream.
Optional CryoCooler enables the start of an analysis at sub-ambient temperature.
Hardware Advantages:
The AutoChem II features stainless-steel construction, fully automated flow and pressure control, an embedded microprocessor with real-time control, and an intuitive graphical user interface for reactor control. A temperature-controlled, stainless-steel flow path provides an inert and stable operating environment, and reduces the potential for condensation in the flow path.
Analysis gas may be introduced to the carrier stream by a precision automated loop.
Thermal conductivity detector (TCD) is capable of detecting minute differences in the concentration of gases flowing into and out of the sample reactor. Its corrosion-resistant filaments are operated at constant temperature to prevent thermal runaway.
The extremely low volume of the internal plumbing minimizes peak spreading and significantly enhances peak resolution.
The AutoChem II Technique:
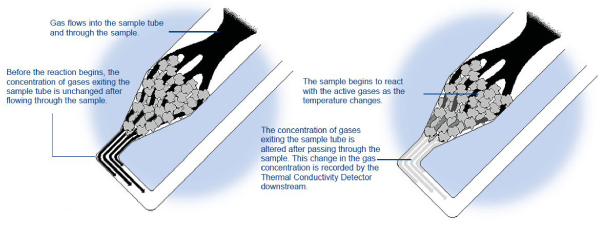
During the TPR, a metal oxide reacts with hydrogen to form a pure metal. This reaction is referred to as a reduction; for example, TPR of a catalyst containing platinum. Argon, which has a very low relative thermal conductivity, is used as a component in the carrier gas.
It is blended in a fixed proportion with hydrogen, the reducing gas with a much higher thermal conductivity. Then the gas mixture flows through the analyzer, through the sample, and past the detector. When the hydrogen and argon gas blend begins flowing over the sample, a baseline reading is established by the detector.
This baseline is established at a low enough temperature so that no reduction of the sample occurs. The baseline level indicated by the detector is that of the thermal conductivity of the two gases in their fixed proportion.
The temperature is then raised and, when a critical temperature is reached, hydrogen atoms in the gas flow react with the sample, forming H2O molecules. The H2O molecules are removed from the gas stream using a cold trap.
As a result, the amount of hydrogen in the argon/hydrogen gas blend inside the analyzer decreases, and the proportion between the two gases shifts in the direction of argon, as does the mixture’s thermal conductivity.
Since argon has a lower thermal conductivity than hydrogen, the mixture’s thermal conductivity consequently decreases. The flowing gas removes heat from the filament more slowly, requiring less electricity to maintain a constant filament temperature.
The instrument records the electrical demand as it changes (this is called the detector signal). The detector signal is recorded continuously over a range of temperatures. When these readings are graphed, the data form one or more peaks. Peaks can be positive or negative.
AutoChem II 2920 Applications
Chemisorption:
Chemical adsorption is an interaction much stronger than physical adsorption. In fact, the interaction is an actual chemical bond where electrons are shared between the gas and the solid surface. While physical adsorption takes place on all surfaces if temperature and pressure conditions are favorable, chemisorption only occurs on certain surfaces and only if these surfaces are clean. Chemisorption, unlike physisorption, ceases when the adsorbate can no longer make direct contact with the surface; it is therefore a single layer process.
Catalyst
The active surface area and porous tructure of catalysts have a great influence on production rates. Limiting the pore size allows only molecules of desired sizes to enter and leave; creating a selective catalyst that will produce primarily the desired product. Chemisorption experiments are valuable for the selection of catalysts for a particular purpose, qualification of catalyst vendors, and the testing of catalyst performance over time to establish when the catalyst should be reactivated or replaced.
Fuel Cells
Platinum-based catalysts including Pt/C, PtRu/C, and PtRuIr/C are often characterized by temperature-programmed reduction to determine the number of oxide phases and pulse chemisorption to calculate:
- Metal surface area
- Metal dispersion
- Average crystallite size
Partial Oxidation
Manganese, cobalt, bismuth, iron, copper, and silver catalysts used for the gas-phase oxidation of ammonia, methane, ethylene, and propylene are characterized using:
- Temperature-programmed oxidation
- Temperature-programmed desorption
- Heat of desorption of oxygen
- Heat of dissociation of oxygen
Catalytic Cracking
Acid catalysts such as zeolites are used to convert large hydrocarbons to gasoline and diesel fuel. The characterization of these materials includes:
- Ammonia chemisorption
- Temperature-programmed desorption of ammonia
- Temperature-programmed decomposition of alkyl amines
- Temperature-programmed desorption of aromatic amines
Catalytic Reforming
Catalysts containing platinum, rhenium, tin, etc. on silica, alumina, or silica-alumina are used for the production of hydrogen, aromatics, and olefins. These catalysts are commonly characterized to determine:
- Metal surface area
- Metal dispersion
- Average crystallite size
Isomerization
Catalysts such as small-pore zeolites (mordenite and ZSM-5) containing noble metals (typically platinum) are used to convert linear paraffins to branched paraffins. This increases the octane number and value for blending gasoline and improves the low temperature flow properties of oil. The characterization of these materials includes:
- Temperature-programmed reduction
- Pulse chemisorption
Hydrocracking, Hydrodesulfurization, and Hydrodenitrogenation
Hydrocracking catalysts typically composed of metal sulfides (nickel, tungsten, cobalt, and molybdenum) are used for processing feeds containing polycyclic aromatics that are not suitable for typical catalytic cracking processes. Hydrodesulphurization and hydrodenitrogenation are used for removing sulfur and nitrogen respectively from petroleum feeds. The characterization of these materials includes:
- Temperature-programmed reduction
- Oxygen pulse chemisorption
Fischer-Tropsch Synthesis
Cobalt, iron, etc. based catalysts are used to convert syngas (carbon monoxide and hydrogen) to hydrocarbons larger than methane. These hydrocarbons are rich in hydrogen and do not contain sulfur or nitrogen. The characterization of these materials includes:
- Temperature-programmed desorption
- Pulse chemisorption
AutoChem II 2920 Software Features:
The easy-to-use AutoChem II software utilizes a Windows® interface that includes Wizards and applications to help plan, launch, and control the analysis.
You can collect, organize, archive and reduce raw data, and store standardized sample information and analysis conditions for easy access during later applications. Finished reports may be generated to screen, paper, or data transfer channels. Features include cut-and-paste graphics, scalable-and-editable graphs, and customizable reports.
Set up analysis protocol sequencing from any number of preprogrammed experiments or create a customized sequence. The user can easily select the pretreatment and analysis task and specify criteria such as temperature ramp rates, gas flow rates, and data measurement intervals in the desired sequence. Modifications may be made to the analysis protocol at any time, even during analysis.
The instrument schematic screen displays the instrument’s current operating status, including the availability of analysis and pretreatment gases and vapors, direction of the gas flow, and TCD reading.
Numerous plots can be overlaid for easy comparison of different samples or for comparison of different data reduction techniques applied to the same sample.
Exportable data tables provide for merging and comparing data from other sources in a single spreadsheet file.
Data Reduction and Reporting – Powerful Peak Editor:
Fully integrated, interactive peak editor package enables the user to evaluate results quickly and easily, edit peaks, and produce reports that reflect specific needs. Adjusting peak boundaries is a matter of simply pointing and clicking. The Peak Editor can also be used to deconvolute overlapping peaks. The peak deconvolution is a simple-to-use option on the peak space editor that allows the user to maximize the information.
The AutoChem II Also Includes:
- Ten user-configurable graphical reports
- BET, Langmuir, and total pore volume
- Pulse chemisorption, % dispersion, metal surface area, and crystallite size
- First-order kinetics, heat of desorption, and activation energy
- Integration of mass spectrometer data files
- AutoChem II 2920 Data Reduction and Reports
Cirrus 3 Quadrupole Mass Spectrometer
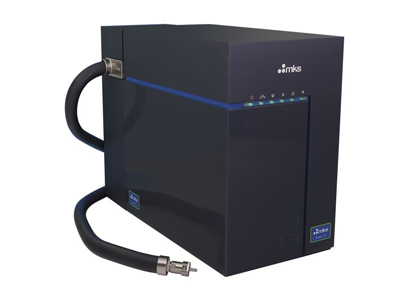
Atmospheric Pressure Gas Monitoring
Building on proven Cirrus Quadrupole Mass Spectrometry technology, the Cirrus 3 combines state-of-the-art performance in compact benchtop and rack-mounted formats. With a heated capillary inlet and fast scan speed (250 points per second), gas compositions can be tracked over wide dynamic range (ppb to percentage levels) more reliably.
- Monitors multiple gas species from trace levels (ppb) to high abundance
- Fast response – 250 data points per second & capillary inlet heated up to 300°C
- Precise and stable user-defined temperature control with enhanced oven and capillary designs
- Detect gases up to 300 amu. High resolution options (1-100HP)
- Recipe-driven Process Eye™ Professional supports gas monitoring and quantitation applications
- Fast and Reproducible Data
Cirrus systems are based on Quadrupole Mass Spectrometry, widely acknowledged as a preferred platform technology for many atmospheric pressure gas analysis applications. The Cirrus 3 system, with its improved temperature control and compact design, provides high levels of performance and robustness in space-efficient and flexible configurations that are ideal for a wide range of analytical applications.
Precision engineered to provide fast and reproducible data, Cirrus 3 can accurately detect and quantify gases and gas mixtures, from one or more sampling locations with a single instrument. Gas composition can be monitored over a wide dynamic range, from percentage levels down to the sub ppm range.
Cirrus 3 is an ideal choice for atmospheric gas analysis whether you work in a research setting or a manufacturing environment. By combining Process Eye Professional software with MKS technical support, Cirrus can be integrated, optimized, and automated to your precise specifications. Ultimately, users across your organization realize greater benefits of the power of quadrupole mass spectrometry.
Quadrupole Analyzer
At the heart of every Cirrus 3 system is a precision-built quadrupole analyzer incorporating a closed ion source, a triple mass filter, and a dual (Faraday and Secondary Electron Multiplier) detector system. This analyzer configuration is selected to optimize sensitivity and longterm performance stability
The Cirrus 3 system enables the AutoChem II 2920 and AutoChem 2950 HP to function as multi-component microreactors. Cirrus 3 software includes Process Eye™ Professional which controls analyzer data collection and monitors real-time data and analyzer status.
A Recipe wizard helps create and configure analysis conditions. The Micromeritics/Cirrus interface software runs inside Process Eye Professional and is accessed via its own menu.
This interface enables the user to control the analyzer via recipes which can also be saved for future use. The interface allows the user to collect data automatically from the AutoChem, customize Peak Jump recipes, access standard operations, calibrate detectors, and scale the AutoChem sample thermocouple signal.
Data integration with AutoChem II 2920 and AutoChem 2950 HP
- MS data may be analyzed using the Micromeritics Peak Editor that allows signal deconvoution (peak fitting), signal integration, and smoothing.
- The AutoChem software may be used to create MS calibrations and convert raw signals to quantitative analyses.
- Data may be used directly in AutoChem characterization reports: dispersion, active area, kinetics, crystallite size.
Features and Benefits:
- Monitors multiple gas species over a wide dynamic range of composition at atmospheric pressure
- Compact, modular design for ease of serviceability and maintenance
- Direct Ethernet interface – fully network compatible
- Recipe driven Process Eye™ Professional software for automated operation and calibration
- Fast response, silica capillary inlet heated to 150° C
For sampling different gas conditions, inlet options available are:
- Stainless steel capillary
- Low flow capillaries
- Multi-stream inlets
- Automated variable pressure inlet
Applications
- Monitoring of trace contaminants in process gas
- Catalyst studies
- Fuel cell monitoring and development
- Heat treatment/furnace monitoring
- Membrane studies
- Glove box gas monitoring
- Lamp manufacture
- Gas supply monitoring (cylinder checks and special gas production)
- Freon detection and identification
- Environmental monitoring. Thermal analysis – TGA, DTA
- Fermentation process monitoring